VVV: Variare la
Velocità delle Ventole
|
La
seconda puntata del tutorial sulle ventole PC.
Da
quanto visto finora dovrebbero essere chiare alcune differenze sostanziali tra
i motori a campo rotante in corrente alternata e questi BLDC utilizzati nelle
piccole ventole per PC.
Pur essendo necessario in entrambi una "rotazione" del campo
magnetico sullo statore che trascini con se in rotazione il rotore, il campo
magnetico generato da correnti alternate sinusoidali ha un andamento molto
differente da quello generato da impulsi di corrente.
Nel
motore "base" di G. Ferraris le due correnti sinusoidali sono
sfasate tra di loro nel tempo dello stesso angolo con cui sono sfasate nello
spazio le bobine. Il campo magnetico di una coppia polare passa da un massimo
ad un minimo di senso opposto secondo una progressione "uniforme",
determinata dall' andamento sinusoidale della corrente. E il campo magnetico
alla coppia polare successiva segue l' andamento del primo con uno sfasamento
temporale che origina un fluido ruotare delle polarità.
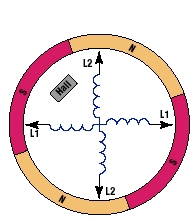 |
Nel motore bi fase delle ventole una coppia polare
è alimentata al massimo, da un impulso di corrente, mentre la
coppia successiva è del tutto non alimentata; dopo di che si
scambia la situazione: il campo non circola fluidamente attorno allo
statore, ma ora è qua, ora è la là, comandato da un' onda quadra
che passa dallo zero al massimo senza intermedi. |
Nel
campo sinusoidale il "ruotare" è determinato dallo sfasamento tra
le due correnti che alimentano le bobine.
Nel motore delle ventole la "rotazione" è determinata dal
succedersi a scatti di bobine alimentate e non alimentate.
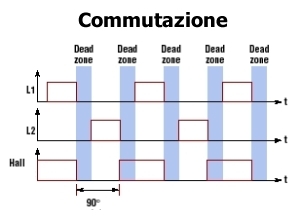 |
Tra l' altro, un "campo
rotante" creato da impulsi richiede la presenza di tempi morti
(dead zone) in cui è opportuno che le bobine non siano alimentate
contemporaneamente onde evitare impuntamenti nel passaggio delle
coppie polari del magnete in rotazione davanti alle espansioni.
dello statore.
In ogni caso, per un angolo di 90
gradi, solamente una coppia polare fornisce il campo magnetico e
questo si traduce in un movimento " a strappi" compensato
dall' inerzia della massa rotante che fa da "accumulatore"
di energia.
|
Si
può ben comprendere come siamo ben lontani dalla fluidità di un motore in
alternata sinusoidale.
Certamente, aumentando il numero di coppie polari, tanto nel motore
"sinusoidale" quanto nel BLDC si ha un miglioramento del rendimento,
in quanto il trasferimento di energia dal campo magnetico alla rotazione
meccanica è più costante e lascia meno all' inerzia; in pratica si verifica
che la situazione trifase (tre sinusoidi sfasate di 120 gradi) costituiscono
il migliore compromesso tra complessità costruttiva e prestazione.
Nei
motori BLDC, però questo "three-phase power" è meno marcato,
in quanto l' alimentazione non è sinusoidale, ma impulsiva e presenta quindi
problematiche differenti.
Ciò non toglie che motori in cui necessita sia una potenza maggiori a parità
di volume, sia la possibilità di un controllo reale della velocità del rotore
vengano realizzati in tecnica trifase anche nel campo dei brushless.
.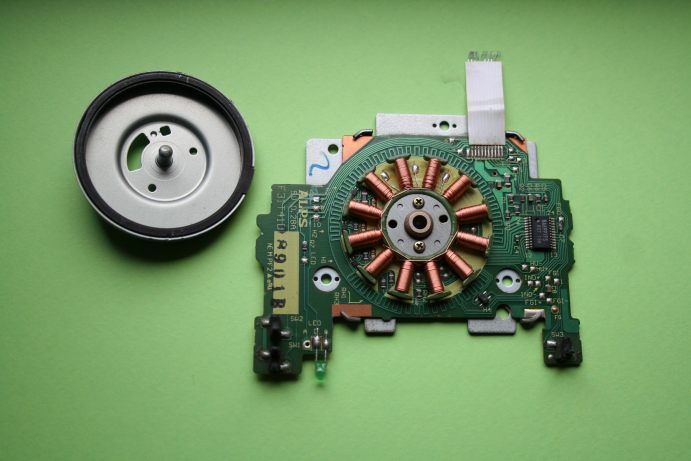
Ad
esempio, questo è il tipico motore di rotazione di un drive CD-DVD.
Praticamente del tutto integrato nel circuito stampato di supporto, viene
controllato da un apposito chip (in questo caso il BA6991 di Rhom) che,
assieme a pochi altri componenti, consente una reale regolazione della velocità,
oltre a fornire sufficiente energia per portare in rotazione il piattello del
CD, sotto controllo del microprocessore principale del drive.
Anche qui è presente un sensore di Hall per il segnale tachimetrico e di
sincronismo (nella foto il componente a 4 pin a ore 4 rispetto allo statore).
Sul rotore, che qui è completamente coperto da una cappa metallica amagnetica
per isolare quanto possibile i disturbi creati dalla commutazione sulle
bobine, si nota una parte di questa copertura in cui è stata ricavata una
fessura dove il magnete sporge lievemente all' esterno con una espansione, per
azionare il sensore di Hall.
L' insieme della realizzazione è ben più elaborato e complesso (e costoso)
di quello bi-phase delle ventole finora viste.
In
ogni caso dovrebbe essere chiaro che, a differenza dell'esempio sopra esposto,
il motore bi fase delle ventole, se è un
capolavoro di semplicità costruttiva, non ha nella sua elettronica un vero e
proprio "controllo".
L' elettronica, infatti, non ha funzioni di "controllo", ma è solo
il minimo essenziale per temporizzare gli impulsi di corrente alle bobine.
Anche il sensore di Hall ha una funzione di "controllo" o feedback
grosso modo pari a quella di un fine corsa.
Non esiste alcun sistema per "controllare" la velocità, a parte il
bilanciamento naturale tra energia fornita e resistenze da vincere per la
rotazione delle pale; quindi la velocità è controllabile dall' esterno solo
con la variazione della tensione di alimentazione. Riducendo la tensione di
alimentazione, nei limiti che consentono ai componenti elettronici di
funzionare correttamente, si riduce la quantità di energia fornita al campo
magnetico e quindi si costringe il sistema a stabilizzarsi su una velocità di
rotazione minore.
Non esiste, però, un sistema di controllo della coppia e della velocità che
permetta accelerazioni e decelerazioni controllate, ne tanto meno un sistema
che eviti lo stallo e/o consenta un riavvio.
Sia
ben chiaro che non è impossibile implementare un diverso sistema di controllo
più efficace e sofisticato, ma per lo scopo per cui sono costruiti questi
motori non serve; sarebbe solo un aumento di costo.
Il
fatto che in altre applicazioni, come nei motori che trascinano i dischi,
rigidi o ottici, le esigenze di controllabilità siano ben diverse dà origine
a motori realizzati in modo differente e con veri "controller" in
grado di controllare realmente e dettagliatamente il motore.
Però
può capitare di sentire la necessità di regolare anche la velocità delle
ventole PC: questo dipende essenzialmente dal fatto che, a pari
caratteristiche meccaniche, maggiore è la loro velocità, maggiore è la
quantità di aria spostata e quindi maggiore è l' effetto
"raffreddante" (sul quale sarebbe necessaria un' altra discussione
perchè si tratta di un altro di quei fatti che paiono di comune comprensione,
mentre in realtà è fenomeno del tutto mal compreso da troppi).
Il
problema che sorge è il seguente: più velocità, più "fresco", ma
più velocità, più rumore, sia per quello meccanico dovuto alla costruzione
dei supporti, sia, sopratutto, per quello delle pale che "tagliano"
l' aria.
Solamente
una progettazione ed una realizzazione estremamente accurata di ogni
particolare della ventola può portare ad una riduzione sensibile del rumore.
Ma usare tempo e mezzi per la ricerca della migliore curvatura delle pale e l'
impiego di materiali di elevata qualità si scontra sempre con il fattore
costo.
Ne risulta che l' unico modo per avere ventole ragionevolmente silenziose è o
pagarle il giusto prezzo o utilizzarle a velocità ridotta.
Senza
bisogno di "regolatori" questo si può fare scegliendo dai cataloghi
ventole di diametro o di spessore maggiore, ottenendo così lo stesso flusso
d' aria con una velocità minore.
Negli
altri casi si agisce secondo il seguente principio: fino a che la temperatura
è bassa, serve poca circolazione di aria; a mano a mano che la temperatura
sale, sale anche la velocità. Così si avrà un sistema silenzioso fino a che
è usato mediamente in condizioni di limitata dissipazione e diventerà più
rumoroso solo all' aumentare della potenza dissipata.
Variazione
di velocità analogica.
Quanto
detto è un caso tipico di regolazione analogica.
Abbiamo detto che, data la loro struttura, la velocità della ventola può
essere variata solamente variando la tensione di alimentazione (e ricordando
che la riduzione di velocità dovuta alla riduzione della tensione è
conseguente al fatto che si riduce la potenza trasmessa alla girante).
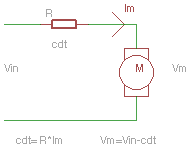 |
Dunque
il sistema più semplice sarebbe quello di inserire una resistenza in serie al
motore: la corrente che lo attraversa, a seconda della resistenza, produce una
caduta di tensione e diminuisce quella disponibile ai capi del motore.
|
La
soluzione, se pur iper semplice ed adeguata a molte situazioni, presenta
alcuni problemi:
1 - sulla resistenza si dissipa una potenza persa in calore, proporzionale
alla corrente che la attraversa
P
= cdt * Im = R * Im2
Non
si tratta di grandi valori, ma comunque è sempre calore in più. Ad esempio,
volendo portare a 9 volt la tensione su una ventola che consuma 100 mA a
quella tensione, sarà necessaria una resistenza da
R
= (Vin - Vm) / Im = (12-9) / 0,1 = 30 ohm
e
della potenza di :
P
= cdt *Im = (12-9) * 0.1 = 0,3 W
e
si potrà usare una 27 o 33 ohm da 1 W.
2 - la corrente assorbita dal motore varia a seconda della tensione con cui è
alimentato.
Per cui il calcolo sopra fatto è valido se la
ventola assorbe 100 mA a 9V. Perchè se assorbe 100 mA a 12V, a 9 V la
corrente sarà minore.
E la potenza assorbita varia anche in funzione della resistenza dell' aria, ma
questa la possiamo ritenere costante.
3 - In ogni caso, con una resistenza di valore fisso possiamo ridurre la
velocità della ventola ad una valore fisso.
Per
ovviare al problema di rendere variabile la velocità possiamo sostituire la
resistenza fissa con una variabile.
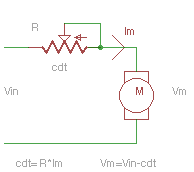 |
Il
problema che si pone qui è la dissipazione sul potenziometro.
La corrente che alimenta una ventola tipica per PC è dell' ordine del
centinaio di milliampere, il che non richiede un reostato da tram, ma non va
bene neppure un potenziometro per audio. Ci vorrà un potenziometro a filo e
questo costa ben di più della ventola stessa.
Nell'
esempio del caso precedente, volendo variare la tensione tra 6 e 12V, il
potenziometro potrà avere un valore di 50 ohm circa e dovrà essere un
elemento a filo da 2W per sicurezza.
|
Possiamo
allora effettuare la regolazione per variazione di tensione attraverso un
regolatore a tre terminali variabile, ad esempio il classico LM317. In questo
caso il potenziometro di regolazione è un trimmer generico e la potenza è
dissipata solo dall' LM. Questa è l'application standard di un componente più
che noto.
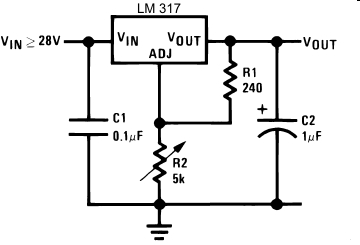
Si presenta però un problema di cui nessuno pare tener conto:
-
in una
situazione del genere il motore da 12V nominali non potrà mai essere
alimentato a 12V data la caduta di tensione sul regolatore (non ci sono nel PC
fonti di tensione superiori ai 12V) e quindi la ventola potrà avere un campo
di regolazione solo inferiore al massimo.
Tensione
massima sul motore = tensione di alimentazione - caduta di tensione sul
regolatore
Per un funzionamento stabile, il costruttore dichiara la necessità di una
differenza tra tensione di alimentazione e tensione di uscita di 3 V, il che
porterebbe la tensione massima sul motore non a 12V, ma a solo 9V.
Questo di per se non è un problema: lo scopo era proprio quello di ridurre la
velocità della ventola e, se proprio occorre disporre anche del massimo della
portata di aria basta impiegare una ventola con caratteristiche di portata
maggiori, in modo da vere quella richiesta anche se l' alimentazione non
arriva a 12V.
Altra
possibilità è utilizzare una classe di regolatori molto più valida ed
attuale rispetto ai vecchi LM317/78xx, ma del tutto trascurata dagli
sperimentatori, ovvero un LDO, ad esempio del genere del MIC2941 che ha una
cdt interna dell' ordine di qualche 250 mV massimi con una corrente di 250 mA.
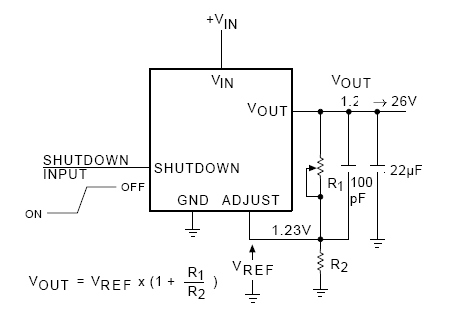 |
Si tratta di un componente in
TO-220, ma a 5 pin, con GND e ADJ separati, oltre ad un pin di
shutdown.
L' application è del tutto
analoga a quella dell' LM317.
Con una caduta dell' ordine del
centinaio di mV la tensione massima applicabile al carico potrà
essere veramente molto vicina a quella di alimentazione.
|
Però,
in tutti questi metodi lineari è richiesta la caduta di tensione, che si
traduce in calore sull' elemento di regolazione; il che vuol dire una certa
quota di energia persa e una ulteriore fonte di calore nel PC.
Per
curiosità, i variatori di velocità delle ventole PC made in China sono
praticamente tutti realizzati semplicemente comandando con un potenziometro la
base di un darlington composto da due NPN che hanno sul collettore il carico
dato dal motore della ventola.
Altri,
più "raffinati", utilizzano semplicemente questo (da un regolatore
Zalman):
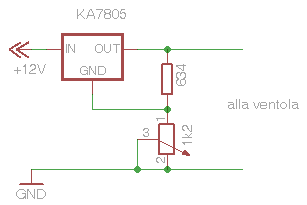 |
Oh,
vertigine del sommo della tecnologia!
Niente condensatori di stabilizzazione, niente diodi di protezione niente
" raffinatezze particolari", ma solo il minimo indispensabile per
fare il lavoro richiesto. Il regolatore a tre terminali, uno dei tanti
equivalenti cinesi della serie 7805/06, assicura una tensione minima di
avviamento della ventola.
Ed è anche più che corretto, perchè è inutile una installazione NASA per
lanciare aerei di carta. |
PWM
Si
può pensare allora ad una regolazione in PWM: viene sempre applicata la
tensione massima, ma a impulsi di ampiezza variabile, sottraendo al carico una
parte della potenza disponibile, potenza sottratta che non viene dissipata in
calore, ma semplicemente non erogata durante i tempi di off del PWM.
Però,
se questo è perfettamente corretto applicandolo ad una resistenza, in cui la
potenza sarà proporzionale al duty cycle del PWM, da 0 al 100%, in un motore
le cose sono diverse.
Sopratutto se il motore è un BLDC come quello descritto.
Quale
è il problema ?
Dovrebbe
essere chiaro che l' alimentazione fornisce potenza al motore solamente quando
le bobine sono eccitate. E qui sono eccitate da impulsi on/off, due per ogni
giro.
Ricapitoliamo:
- una coppia polare viene "accesa": attira il magente-rotore.
- prima che il polo del rotore si allinei con l' espansione polare dello
statore, la corrente alla bobina viene sospesa e viene alimentata la
successiva coppia polare.
- Il rotore, per inerzia, supera il polo inattivo e viene attirato dal
successivo, che ora è attivo. E così via.
Pensiamo all' effetto che ha il PWM su questo gioco di switch; ad esempio, il
PWM sospende l' alimentazione al motore nel momento in cui viene azionata una
bobina; ne deriva che per il tempo di off del PWM quella bobina NON fornisce
alcuna energia al motore, che procede esclusivamente per inerzia, per poi
ricevere una "botta" magnetica non appena una bobina viene
alimentata.
Ci
si può immaginare l' effetto complessivo del sovrapporsi degli impulsi PWM,
dissincroni da quelli del "controller" interno.
Il
primo risultato, il più importante, è che alle basse velocità di rotazione
la tendenza di questo tipo di motore è quella di diventare non meno, ma MOLTO
PIU' rumoroso, con il tipico scampanio che si genera nel gioco pseudo-casuale
di on/off dei transistor interni e del PWM.
In particolare, basse frequenze di PWM sono molto più
"scampanellanti" di alte frequenze; quindi, piuttosto che un PWM a
bassa frequenza, sarà consigliabile una frequenza elevata. Anche se questo può
dare facilmente origine al caratteristico sibilo del battimento tra le
frequenze del PWM e quelle della commutazione.
Inoltre,
il comportamento "acustico" della ventola sottoposta al PWM è del
tutto imprevedibile perchè dipende dalle sua caratteristiche costruttive; e
ci sarà la ventola che sembra il campanello di fine lezione e quella più
educata, ma, a priori, NON discerrnibile e quindi determinabile solo dopo
prove pratiche. Molto aleatorio.
Ci
sarebbe un sistema per rendere efficace un PWM: quello di sincronizzarsi con
lo switch interno e parzializzare non a caso, ma solamente durante il tempo di
on delle bobine.
La cosa però è poco fattibile, sia per la complessità del circuito da
implementare, sia per il problema della non uniformità delle caratteristiche
costruttive, sia perchè, dato che il motore non ha nessun tipo di controller
gestibile dall' esterno, il ciclo di switch dei due transistor è legato
esclusivamente alle caratteristiche costruttive e rilevabile esternamente in
modo grossolano solo attraverso il segnale tachimetrico.
Poco fattibile, non impossibile: in una esercitazione di mechatronica si è
posto un problema simile e trovata una soluzione, ma, come al solito,
assolutamente impropria dal punto di vista economico.
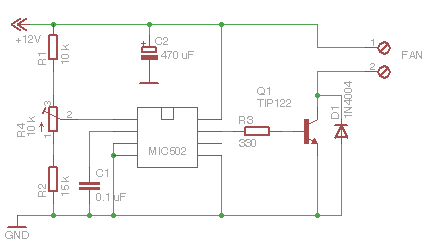 |
Un
altro problema riguarda la forma più semplice di switch PWM, che è
quella con un transistor NPN o MOSFET N che interrompe il polo negativo del
carico.
MIC502 è un PWM controller
di Micrel e risolve il problema meglio del solito 555. |
Funziona, ma nessuno pare tener presente un altro fattore: ricordando come è
realizzata l' uscita tachimetrica, ci si accorge subito che con questo modo di
PWM il segnale tacho è del tutto in palla, diventando un mix tra il segnale
del PWM e quello della commutazione interna del motore, e quindi del tutto
inutilizzabile. Quando il transistor interruttore è aperto, non arriva
tensione alla ventola e quindi l' open collector interno del tacho è separato
dal GND.
Ultimo
punto riguarda il fatto che con un PWM on/off sul carico si ottiene una
corrente a impulsi sull' intero sviluppo dei cavi di collegamento tra la
ventola e il regolatore, con la corrispondente generazione di uno spettro di
disturbo elettromagnetico la cui energia è proporzionale alla corrente che
viene interrotta. La corrente non è elevata, ma anche solo un centinaio di mA
commutati a onda quadra, a cui si somma il segnale di disturbo generato dalla
ventola stessa, è facilmente avvertibile con un ricevitore radio posto nelle
vicinanze.
Apriamo
una parentesi a riguardo: i motori brushless, non hanno le brushes, ma non per
questo sono esenti dalla generazione di disturbo elettromagnetico. In questo
caso non si avrà scintilla sulle spazzole, ma la rapida commutazione della
corrente nelle bobine crea comunque un segnale che si sovrappone alla tensione
di alimentazione.
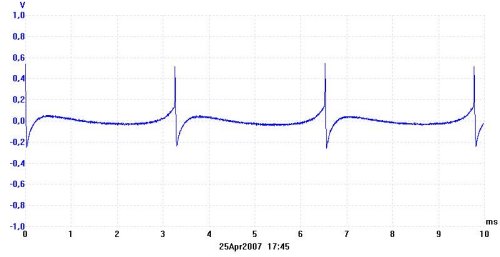 |
Questa è la tensione di ripple
misurata ai capi di una ventola comune.
Si nota bene l' effetto della
commutazione che somma più di 500 mV di rumore.
Questo non da alcun problema al
resto del circuito, in cui gli spikes dovuti al funzionamento
digitale sono ben più imponenti.
In ogni caso, l' aggiunta in parallelo ai morsetti del motore di un
condensatore elettrolitico di piccola capacità è sufficiente a
ridurre decisamente il ripple.
|
In un mondo afflitto da una "atmosfera" densa di segnali
elettromagnetici da fare impressione, l' aggiungerne altri, anche se di
piccola potenza, non è un' opera pia.
E, anche se di piccola potenza, in un piccolo raggio sono fonte di disturbo
per altre apparecchiature, dalle TV alle radio e perfino agli Hi-fi (e ogni
radioamatore ha tribolato a volte non poco per far entrare nella sua stazione
una fonte di disturbi così efficace come il PC).
Anche
se interrompiamo il polo positivo il segnale tacho viene disturbato e comunque
il problema del battimento a bassa velocità con relativo rumore è sempre
presente.
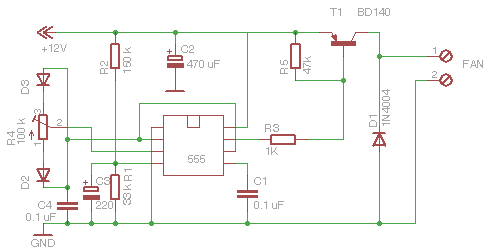
Quindi,
anche se apparentemente in accordo con lo stato dell' arte dell' elettronica,
la regolazione in PWM così imposta non presenta alcun vantaggio, se non una
piccola riduzione dei pochi milliwatt persi sulla regolazione lineare, contro
probabili e seri svantaggi di rumore meccanico ed elettrico. Inoltre si tratta
di circuiti il cui costo è pari o supera quello della ventola stessa.
In
PWM, l' unica via possibile per regolare questi motori ed eliminare i problemi
evidenziati è quella di utilizzare uno switch high-side, che generalmente si
realizza con un MOSFET P, seguito da un gruppo D/L/C a creare uno step-down,
ovvero a regolare in PWM non la corrente che passa nel motore con un brutale
on/off, ma a costituire un regolatore di tensione.
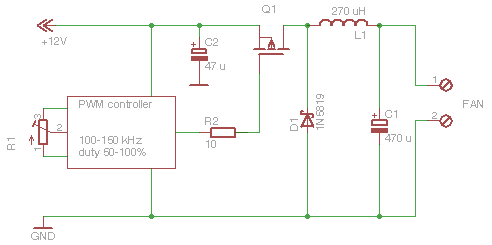
Il
PWM controller può essere un chip dedicato, come i vari UC o il già visto di
Micrel, ma anche il solito 555.
Non serve alcun dissipatore per il MOSFET, data la bassa corrente erogata e si
può usare anche un componente in EXDIP del genere IRFD9110 o simile, anche in
smd.
Da
notare che il duty cycle viene limitata in basso al 50/55% per evitare che
sulla ventola sia applicata una tensione troppo bassa per l' avviamento.
A
questo proposito è utile ricordare, di nuovo, a chi intenda fare un
regolatore di velocità per le ventole PC che il limite minimo della tensione
applicabile per avere un sicuro avviamento è un punto del tutto trascurato da
gran parte degli schemi presenti sul web, proprio perchè manca la conoscenza
di come funziona il motore.
Infatti
si verificano due punti che, se non giustamente considerati, portano
irrimediabilmente alla ventola ferma:
1 - la ventola a 12V, una volta in rotazione, si mantiene in rotazione a bassa
velocità anche per tensioni al di sotto dei 6V. Però si potrà osservare con
facilità che, se la ventola avviata gira ancora con 4V, da fermo con 4V non
parte !!!
2 - la ventola, se nuova, ha il minimo di attriti. Dopo ore di lavoro e chili
di polvere, la situazione è diversa. Per cui, se ho verificato che la ventola
parte con certezza, a nuovo, con 5V, è quanto mai difficile che questa
tensione sia ancora sufficiente già dopo un po' di ore di lavoro.
Solitamente
si parte dal presupposto di sicurezza di non fornire mai meno di metà della
tensione nominale, anche se con ventole a 12V, 6- 7V sono un limite minimo più
sicuro.
E
se la ventola è bloccata ? Semplicemente non gira.
Elettricamente, se si è seguito quanto fino ad ora detto, dovrebbe essere
chiaro che, a rotore fermo e tensione presente, uno dei due transistor conduce
e l' altro no, per cui si avrà una bobina eccitata, che contribuisce a
mantenere in stallo la girante e basta. Se i transistor sono sufficientemente
dimensionati, non succede alcun guaio; ci sarà solo una dissipazione di
calore in quanto tutta la corrente attraverserà l' avvolgimento. Trattandosi
però di correnti piccole, si spera che anche i semiconduttori, fondi di
magazzino, usati in queste applicazioni siano sufficientemente dimensionati.
Sempre
parlando di limiti, l' idea di sovra alimentare le ventole per ottenere una
maggiore velocità pare intelligente (caspita, ho capito come funziona il
motore: meno tensione, meno velocità, ma più tensione, più velocità) è,
invece, una bruttissima idea perchè ha due immediate conseguenze:
1 - accorcia drammaticamente la vita delle parti meccaniche già di per sè
limitata dalla qualità non eccelsa dei materiali
2 - porta un reale rischio di bruciatura della giunzione dei transistor per l'
aumento della sovra tensione durante le commutazioni.
Se si vuole "più aria" basta scegliere dai cataloghi una ventola
con una portata maggiore.
Oltre
a questo va puntualizzato che nell' alimentatore PC non ci sono tensioni
superiori a 12V.
Il furbetto dell' alimentatorino ottiene un magico 17 V o un esoterico 15,3 V
collegando il carico rispettivamente tra il +12 e il -5 o tra il +3.3 e il
-12.
Che è un' altra sciocchezza al cubo, in quanto l' alimentatore PC non è previsto
per erogare correnti incrociate sui vari rami (le quali non rientrerebbero nel
sistema di stabilizzazione), oltre al fatto che i rami negativi sono ottenuti
spesso con tre terminali tipo 7905/7912 praticamente privi di radiatore o con
una derivazione dal trasformatore principale raddrizzata con piccoli diodi.
Per fortuna di solito non succede niente, non per la genialità del furbetto,
bensì perchè le correnti assorbite da una ventola sono assai piccole
rispetto quelle che gestisce l' alimentatore. Ma se venisse in mente di
prelevare correnti maggiori, il fil di fumo è in agguato.
Ovvero si può anche attraversare le rotaie quando il passaggio a livello è
abbassato, ma avendo cognizione di quello che si sta facendo.
Regolare
in funzione della temperatura
Se
rendiamo la ventola regolabile manualmente, ci troviamo di fronte ad una
specie di non senso, dato che la velocità della ventola dovrebbe essere
proporzionale alla temperatura; ci si troverebbe costretti ad fare da
"controller" in una regolazione manuale temperatura/velocità. Non
può arrangiarsi l' automatismo da se ?
Certo
che può. E' ormai normale avere negli alimentatori PC un sistema di controllo
proporzionale della velocità in funzione della temperatura interna.
Anche qui, in generale, non ci troviamo di fronte a circuiti con
microcontroller DSP e curve di risposta calibrate, ma cose del genere:
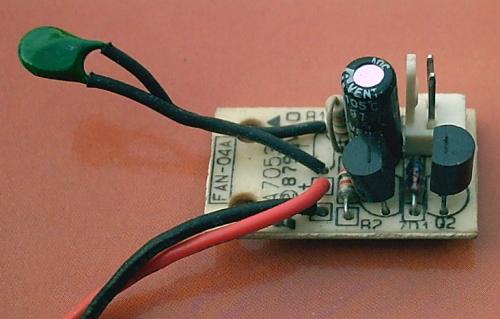
Che,
in pratica, sono così:
 |
Sostanzialmente
la resistenza di un darlington viene ridotta in funzione del valore della NTC,
fino a portarlo in saturazione oltre una certa temperatura. Ne risulta una
variazione tra circa metà tensione e il massimo per temperature tra pochi
gradi e 40-60 gradi Cosa faccia il circuito al di sotto dello zero non saprei,
ma le specifiche di funzionamento dell' alimentatore (o regolatore o ventola o
PC) parlano chiaramente di range di temperatura commerciali e quindi chi vuole
far funzionare correttamente il PC in inverno sul K2 dovrà attrezzarsi
opportunamente con qualcosa a norme MIL.
Anche
qui si tratta di un circuito del tutto "funzionale", privo di
qualsiasi raffinatezza e il cui funzionamento senza tarature si basa solo
sull' equilibrio dei componenti scelti. Si
tratta, come per i motori delle ventole, di cui sono la controparte, di
circuiti che-meno-di-così-non-si-può, però, nel loro piccolo, funzionano. |
Si
trova anche qualcosa di più complesso, come questo circuito in cui, oltre al
controllo della velocità, c'è anche il controllo dello stallo con relativo
allarme e avviamento di una ventola di emergenza. Si nota bene il cavo
inguainato della NTC (solito elemento cinese da 10 K). Il circuito è del tutto convenzionale, con operazionali come amplificatori.
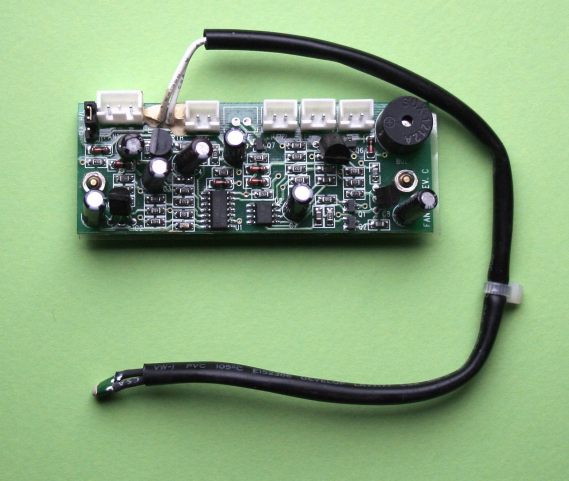
Ma
sono casi abbastanza rari, dedicati ai sistemi non consumer. Per curiosità,
il circuito in foto fa parte di un sistema di allarme e backup ventole all'
interno di una alimentazione per server (Ablecom), dove la necessità di un
ordine maggiore di sicurezza e il costo generale giustificano una
complicazione del sistema di gestione delle ventole.
Le ventole termo controllate.
Quale è realmente lo scoglio da superare ? E'
il fatto che il motore delle ventole così realizzato NON ha alcun modo
efficace per essere controllato dall' esterno !
Per fare qualcosa di efficiente occorre agire all' interno.
Sono stati quindi realizzati degli integrati che "controllano" le
due fasi della ventola in funzione del segnale che arriva da un sensore di
temperatura collegato alla ventola stessa.
Questo
è un esempio di applicazione di un controller Zetex, che ricalca la solita
configurazione a due open collector:
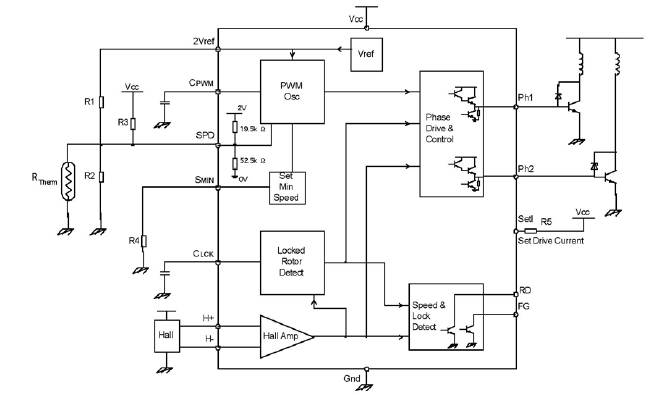
Il
controller diventa ovviamente più complesso e utilizza la variazione del
valore del termistore per un controllo in PWM dei transistor in uscita
przializzando la fase on di alimentazione delle bobine.
Una
raffinatezza: oltre al segnale tachimetrico (FG) viene generato anche un
allarme (RD) in caso di blocco del rotore. Inoltre è regolabile con una
resistenza esterna la velocità minima (R4), per evitare lo stallo da tensione
troppo bassa, come già spiegato in precedenza.
Essendo
il "controller" interno alla ventola sono eliminati tutti i problemi
di cui sopra.
Salvo che non sempre si tratta di elementi realmente silenziosi o la loro
curva di regolazione, che non è accessibile, non è detto sia la più
adeguata ad una certa applicazione.
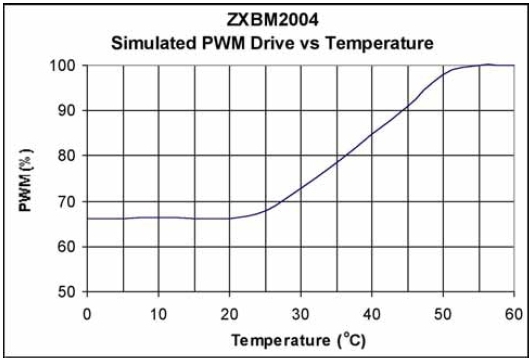
Sarà
spesso necessario bilanciare la regolazione con il posizionamento opportuno
del sensore di temperatura, dove possibile.
Per un filo in più...
Ovvero una soluzione con gran dispendio di
tecnologia per risparmiare pochi milliwatt.
In
tempo di penuria energetica, dove i richiami al risparmio puntano assai
spesso, piuttosto che sul risparmiamo a carico nostro, sul
risparmiamo-a-carico-degli-altri, anche i PC sono colpiti da questa tendenza.
Dopo aver abolito l' interruttore, passando da AT ad ATX, in favore del
pulsante e del PC-sempre-acceso (dove sta il risparmio energetico ?), a consumare in
stand-by svariati watt a cos phi pazzeschi (tipico 0.2), ci si è accorti che,
visti i milioni di PC esistenti, forse qualcosa si poteva fare anche lì. E se
adesso con le nuove tecnologie 85+ lo standby c'è sempre (vuoi mettere
accendere l' apparecchio, PC o TV, dal telecomando stando in poltrona alla
Simpson ?), si è finalmente puntato ad ottenere sistemi che siano in qualche
modo diversi dalle stufe (Pentium Prescott docet).
Ma scaldano comunque ancora in abbondanza e le ventole sono sempre necessarie
(e vorrei vedere: con VGA che ciucciano 200W e più, alla faccia del risparmio
energetico...)..
Ora,
le ventole non solo consumano energia, ma fanno rumore e questo è un problema
più sentito del precedente. Aumentando la voracità energetica dei sistemi ci
si è trovati ad un certo punto ad avere la necessità di far circolare molta
aria e quindi avere ventole veloci e in quantità. Il PC è diventato rumoroso
come un jet al decollo.
Questo ha portato l' utente a cominciare a trovare la cosa decisamente
eccessiva e spinto (anche se a gran fatica...) i costruttori a cercare
soluzioni.
In
sostanza, il ragionamento è semplice: non ha senso che la ventola giri alla
massima velocità sempre; occorre invece che essa possa fornire il volume di
aria adeguato ad ogni condizione termica. Per cui, se CPU e GPU, memoria e
dischi lavorano a bassa energia, basterà un debole flusso d' aria (leggi: una
bassa velocità di rotazione delle ventole, con il relativo contenimento del
rumore), mentre la velocità sarà aumentata in proporzione al calore da
dissipare.
Questo, allo stato attuale della tecnologia non è certo un problema. Il
problema semmai è quello di far rientrare l'innovazione nei termini previsti
dal budget (la cui base è sempre: quello che non c'è, non costa).
In alcuni casi, con le ventole a tre fili (tachimetriche), su schede madri e a
volte anche su schede video, si è provveduto a fornire un controllo, di
solito lineare, della tensione alla ventola in funzione della temperatura del
punto caldo che devono raffreddare. Ma, ovviamente, avere altre sorgenti di
calore perso sui regolatori non era l' optimum e un PWM sul carico, come
detto, diventava una fonte di disturbi che impedivano le certificazioni di
compatibilità elettromagnetica europea e FCC americana.
Dunque, ne è derivata una soluzione differente: le ventole a 4 fili.
Pin |
Funzione |
Colore del cavo |
Connettore MOLEX |
1 |
GND |
Nero |
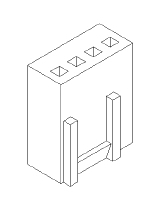 |
 |
2 |
12V |
Giallo o Rosso |
3 |
Tacho |
Verde o Bianco |
4 |
PWM |
Blu |
In
cosa consiste la differenza? Semplicemente nella presenza di un filo in più,
che porta un segnale PWM da un controller sulla scheda madre ad un controller
interno alla ventola.
Ne è nata una ventola che, costruttivamente, resta ancorata ad uno schema
identico a quello visto finora, il che permette di mantenere il sistema
produttivo delle parti elettromeccaniche (bobine sul nucleo a 4 espansioni
polari, rotore con il magnete cilindrico, ecc) ormai collaudato (e
ammortizzato...), e che viene dotata di un integrato di controllo molto più
sofisticato dei vari 276/277 e simili.
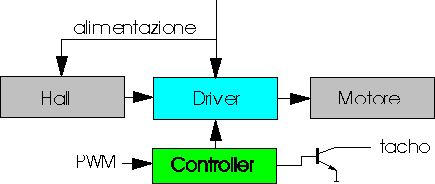
La
struttura del funzionamento è la seguente:
-
sulla scheda madre è installato un integrato dedicato che funge da controller
della ventola
- la ventola fornisce al controller sulla scheda madre il segnale tacho
- il controller rileva il segnale tacho e risponde inviando alla ventola un
segnale di PWM proporzionale ad una temperatura rilevata
- questo segnale PWM viene elaborato dall' integrato a bordo della ventola e
trasformato nella sequenza di impulsi necessari al comando del motore.
Si
potrà poi anche aggiungere un sensore termico on-board per ottenere anche la
possibilità di un termo controllo.
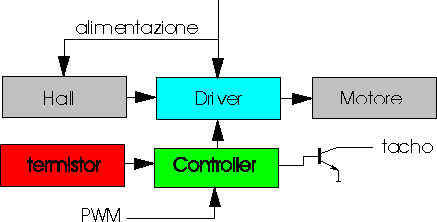
La
differenza con un controllo PWM esterno è molto grande: nella ventola a 4
fili il segnale di PWM che arriva dall' esterno agisce come
"informazione" per il controller interno che provvede a
comandare la bobina del motore al meglio.
Non ci sono dunque "scampanii" a bassa velocità e l' emissione di
interferenze elettromagnetiche è limitata, essendo la parte di potenza tutta
interna all' anello del magnete, che funge da schermo, supportato in molti
casi da un anello esterno in metallo.
Inoltre è possibile avere una variazione di giri praticamente da zero al
massimo senza alcun rischio di stallo a basse velocità o per aumento della
resistenza; la ventola a 4 fili, se bloccata e poi sbloccata, riparte
immediatamente in quanto il controller, che si accorge dell' assenza del
segnale sul sensore di Hall, cerca di riavviare la rotazione pompando i giusti
impulsi di corrente.
Il
controller sulla scheda madre ha la possibilità di dialogare con il
processore centrale (CPU) e scambiare dati sulla situazione della ventola e
della temperatura, rendendo possibile anche l' impostazione di curve
temperatura/velocità con profili programmabili.
Il
segnale PWM, a livello logico e quindi con corrente minima, ha una frequenza
di molti kHz (tipicamente 25 kHz) e va ad agire su un integrato dedicato posto
all' interno della ventola.
Tra
l' altro è da notare che se per le ventole "ordinarie" gli standard
si sono formati praticamente de facto, per le ventole a 4 fili esiste una
linea guida ufficiale dello standard, consultabile a
http://www.formfactors.org/developer/specs/4_Wire_PWM_Spec.pdf
il
che consente intercambiabilità tra schede e ventole.
Ne deriva una decisa maggiore uniformità di comportamento e una ben più
prevedibile risposta ai segnali di controllo rispetto ai tipi a due e tre
fili. Anche perchè diventa impossibile attenersi allo standard realizzando
circuiti estemporanei ed è richiesta la presenza di uno dei tanti integrati
specializzati.
Dalla
necessità della realizzazione di questi integrati "ad applicationem",
delle relative controparti sulle mainboard e dalla necessità di realizzare
firmware nei BIOS e utilities per i sistemi operativi che gestiscano il tutto,
deriva il sotto titolo iniziale: un grande impegno di tecnologia e risorse per
un pugno di milliwatt! (Ne valeva la pena?).
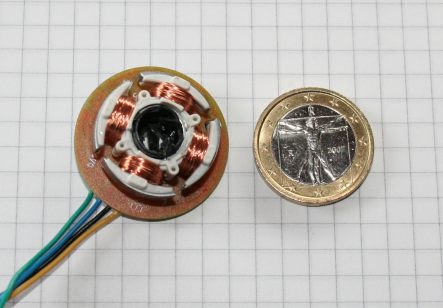 |
Se
apriamo una di queste ventole, a prima vista ci troviamo di fronte ad una
struttura del tutto identica a quanto visto finora.
Questo è un esempio, tratto da una ventola da 70 mm.
Essenzialmente,
in essa resta del tutto invariata la struttura a quattro espansioni polari;
questo consente ai costruttori di utilizzare gran parte delle linee di
montaggio esistenti, ormai ampiamente ammortizzate e quindi sorgenti di utile. |
Guardando
però il lato componenti, forzatamente smd per la piccola superficie
disponibile, le cose sono diverse.
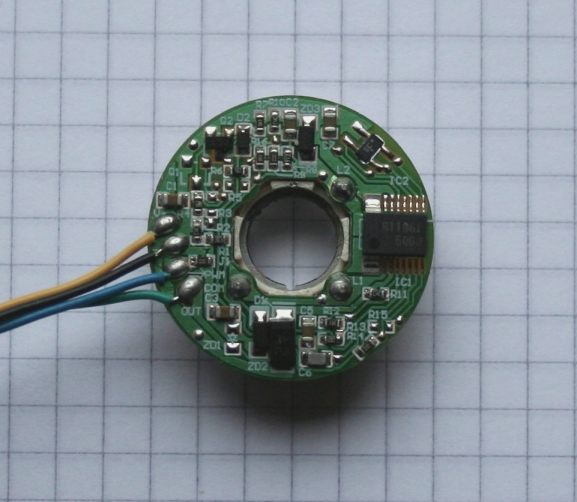
A
parte il numero elevato di componenti, si nota subito il "grosso"
chip a più pin, che è il controller vero e proprio.
Se osserviamo la struttura logica di uno di questi integrati, realizzati
appositamente per questa applicazione, ad es. BD6709 di Rhom o LP11961 di
Sanyo, tanto per citarne due comuni, vediamo che ci sono serie differenze tra
questo e i 276/277 delle ventole viste in precedenza.
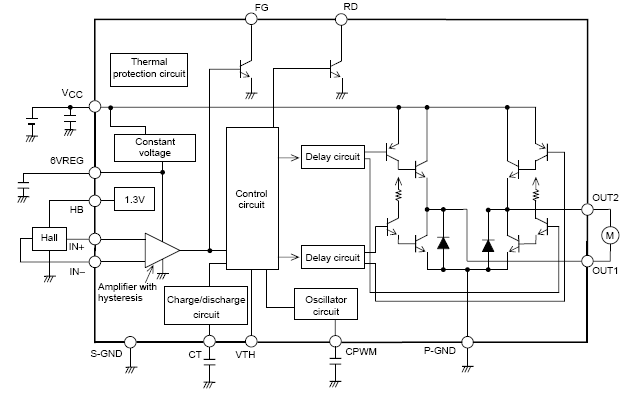
Già
una occhiata superficiale allo schema a blocchi del controller permette di
apprezzare le notevoli differenze, cosa che era meno rilevabile osservando la
struttura del motore.
Se
resta del tutto invariata la struttura a quattro espansioni polari, le bobine,
però, non sono più due ma una sola, suddivisa in quattro parti e avvolte in
verso opposto. Da un motore bi fase siamo passati ad un mono fase. Non è la
soluzione ideale, ma consente, come detto, di mantenere la stesa struttura
meccanica.
Per
comandare il motore viene usato ponte, solitamente a transistor; la potenza
delle ventole è minima, tipicamente 100 mA a 12V, per cui l' integrazione di
MOSFET, che probabilmente comporta costi maggiori in questi circuiti, non è
stata considerata.
La necessità di avere presenti e gestire in ingresso sia il segnale PWM che
il sincronismo dato dal sensore di Hall, sempre presente, da origine a
circuiti piuttosto complessi, con molti componenti che devono giocoforza
essere a montaggio superficiale per poter trovare spazio nella carcassa della
ventola.
Ancora
ben visibile il sensore di Hall (nella foto è il componente a 4 pin poco
sopra il controller), che è componente esterno all' integrato principale.
Il controllo di potenza del PWM e la sua sincronizzazione con gli impulsi
necessari alla rotazione della ventola avviene interamente sotto la gestione
di questo integrato e completamente all' interno della ventola, in rapporto
con il PWM esterno. Al controller sulla scheda madre arriverà il solito
feedback del segnale tacho.
Migliora
così anche l'efficienza del motore e la potenza persa per la regolazione è
ridotta al minimo.
Mentre il rumore, che è determinato praticamente solo dalle caratteristiche
meccaniche della girante e del suo supporto, si riduce quasi a zero a basse
velocità. Va considerato, però, che le ventole a 4 fili correntemente in uso
hanno velocità finali molto alte per permettere un ampio campo di regolazione
e se mandate a pieno regime solo pochi modelli sono ragionevolmente
silenziosi.
Un
esempio della funzione di controllo è data dalla fase di avviamento (POST)
della scheda madre. All' accensione le ventole sono private del segnale PWM e
quindi partono a piena velocità. Poi interviene un diagnostico che verifica
l' arrivo del segnale tachimetrico (se manca c'è un allarme di ventola ferma,
spesso programmabile anche se il tacho è al di sotto di una certa frequenza).
Quindi la CPU agisce sui controller on board perchè adeguino il loro segnale
PWM alla temperatura: essa, inizialmente è bassa, così che le ventole
rapidamente passano ad una velocità minima o addirittura si arrestano del
tutto.
Ed è da notare che questi sistemi possono arrestare completamente la
rotazione della ventola e riavviarla in qualsiasi momento, dato che il
controllo può forzare una coppia sufficiente all' avviamento anche se la
tensione di alimentazione è già presente e la girante è ferma; ovvero la
possibilità di on/off della ventola è completa (mentre abbiamo visto come
sulle ventole a tre fili questo sia assai problematico se non impossibile, non
potendo controllare in alcun modo la coppia e le sequenza di avvio della
rotazione).
Per
inciso, sia pure con qualche limitazione, le ventole a 4 fili possono essere
trattate come ventole a tre fili: se il segnale PWM è assente (quarto filo
non collegato), la ventola gira alla velocità massima e dipende dalla
tensione di alimentazione.
Tanto che il connettore per le ventole a 4 fili è stato realizzato in modo
"compatibile" con quello a tre fili, sia elettricamente che
meccanicamente.
E'
possibile regolare "manualmente" queste ventole al di fuori del PC?
Certamente.
E in modo assai semplice: basta costruire un qualsiasi generatore ad onda
quadra con frequenza fissa attorno ai 25 kHz e PWM variabile. Qui
un esempio di realizzazione semplice.
Da prove fatte i controller interni rispondono bene per frequenze tra 10 e 35
kHz, quindi il fattore "frequenza" dell' oscillatore è scarsamente
importante.
Questo
segnale sarà collegato al quarto filo e determinerà la velocità di
rotazione della ventola, tenendo presente che se si trova floating la velocità
sarà massima.
L'
oscillatore può essere un comune 555 in astabile a frequenza fissa con il
giochino dei diodi per avere PWM variabile oppure qualsiasi altra soluzione
che dia questo risultato.
La tensione del segnale sarà a livello logico 5V, derivata alimentando il 555
dal 12V del PC attraverso un 78L05.
Esiste una estensione della specifica che consente anche la compatibilità con
3.3V. In questo caso all' interno della ventola uno zener limita l' eventuale
applicazione del 5V (il che permetterebbe anche un segnale a 12V, anche se lo
standard non ne parla).
Post scriptum
Sull'
utilità di un articolo come questo qualcuno avanza dubbi: cui prodest ?
In
sostanza, se non vi capiterà mai di usare queste piccole ventole nate per i
PC, probabilmente si tratta solo di un tot di informazioni generiche.
Se
però le utilizzate, la cosa è differente.
Ci pare ovvio che chiunque impieghi qualcosa senza almeno avere una idea
sufficientemente precisa dei principi secondo cui quella cosa funziona ed è
stata costruita, avrà pochissime probabilità di utilizzarla correttamente al
di là un "attaccala-alla-spina-e-premi-il-bottone"
Tanto più se intende farne qualche personalizzazione o applicazione. E il principio vale per ogni cosa, dall' auto al cellulare, dal TV al
frigorifero).
Certamente
non è necessario diventare esperti o progettisti di auto per guidare bene, ma
non esiste il caso di un buon pilota che non sappia a fondo come
funziona la macchina che guida.
E
anche per chi ventole non ne usa, questo "tutorial" ha lo scopo di
attirare l' attenzione su una classe di oggetti apparentemente insignificanti,
ma la cui esistenza è possibile solo a seguito della complessa vicenda
tecnologica del nostro mondo.
Inoltre, anche se presuntuosamente (forse), è un invito a non fermarsi alla
superficie delle cose, ma osservarle e cercarne di capire le ragioni.
|